Discover why electroslag remelting is revolutionizing aerospace manufacturing—enhanced purity, fatigue resistance, and reliability for mission-critical components.
In the high-stakes world of aerospace engineering, where a single material flaw can lead to catastrophic failure, electroslag remelting (ESR) has emerged as a game-changer. This advanced metallurgical process transforms ordinary alloys into ultra-reliable aerospace-grade materials, ensuring components withstand extreme pressures, temperatures, and cyclic stresses. Let’s explore the top five reasons why ESR is now the gold standard for jet engines, landing gear, and other critical aerospace systems.
1. Unmatched Material Purity
ESR eliminates impurities that traditional melting methods leave behind:
- Inclusion Removal: Reduces oxide/sulfide inclusions by 90–95%
- Gas Porosity: Lowers hydrogen content to <1 ppm (vs. 2–5 ppm in vacuum arc remelting)
- Segregation Control: Achieves chemical uniformity with ±0.5% composition variance
Case Study: Rolls-Royce reported a 40% reduction in turbine blade rejections after adopting ESR-processed IN718 superalloy.
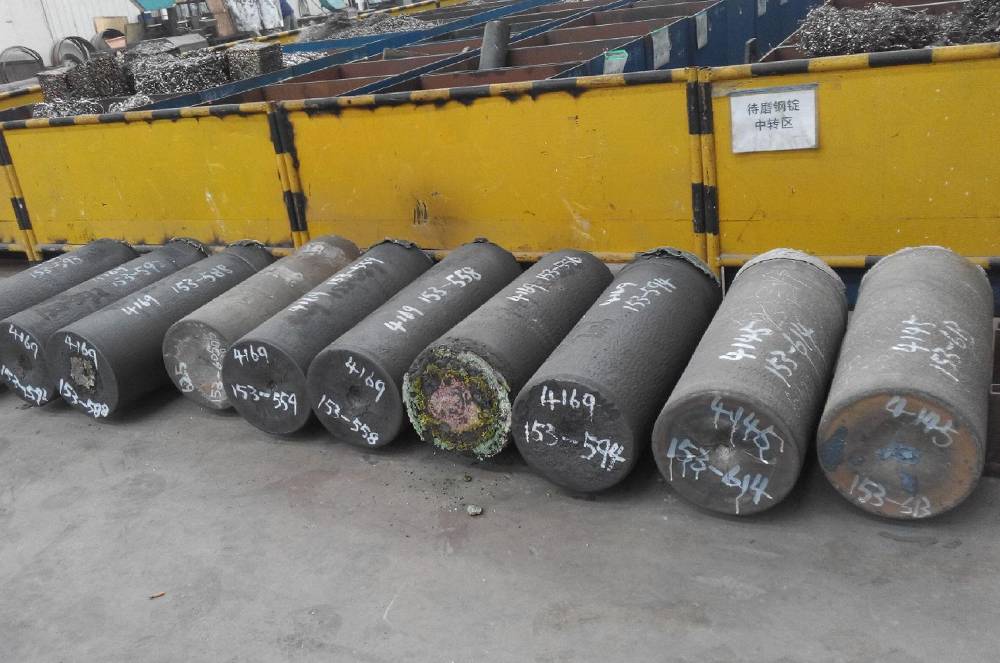
2. Superior Fatigue Resistance
Aircraft components face millions of stress cycles. ESR enhances durability through:
- Directional Solidification: Columnar grain structures resist crack propagation
- Improved Surface Finish: Ra <1.6 μm reduces stress concentration points
- Fatigue Life Gains: ESR-treated Ti-6Al-4V lasts 3–5x longer under cyclic loading
Material | Fatigue Strength (MPa) | Improvement vs. Conventional |
---|---|---|
ESR 300M Steel | 1,450 | +25% |
ESR Ti-6Al-4V | 825 | +35% |
3. Enhanced High-Temperature Performance
Jet engine components operate at 1,500°C+. ESR’s refined microstructure delivers:
- Creep Resistance: 30% longer time-to-failure at 800°C
- Oxidation Stability: Al₂O₃ scale adhesion improved by 50%
- Thermal Fatigue: 20% fewer microcracks in afterburner components
NASA Validation: ESR-processed Haynes 282 showed 15% higher stress rupture life in hypersonic vehicle tests.
4. Reduced Anisotropy
Traditional casting creates directional weaknesses. ESR’s isotropic properties ensure:
- Uniform mechanical properties in all orientations
- Fracture Toughness: KIC values consistent within ±5%
- Machinability: Tool wear reduced by 18% due to homogeneous hardness
5. Cost Efficiency Through Reliability
While ESR adds 10–15% to material costs, it saves exponentially by:
- Extending Service Intervals: Engine overhauls delayed by 8,000–10,000 flight hours
- Cutting Scrap Rates: 70% fewer QA failures in landing gear forgings
- Avoiding Downtime: $500k+/hour savings by preventing in-flight emergencies
ROI Example: Airbus calculated a 12:1 return on ESR adoption for A350 wing spar components.
The ESR Process: How It Works
- Electrode Preparation: Alloy melted into a consumable electrode
- Slag Bath Formation: Fluoride-based slag purifies molten metal
- Controlled Solidification: Water-cooled mold ensures directional grain growth
- Post-Processing: Homogenization heat treatment at 1,200°C
Aerospace Applications Transformed by ESR
Component | ESR Alloy | Key Benefit |
---|---|---|
Turbine Blades | CMSX-4® Single Crystal | 25% higher operating temperatures |
Landing Gear | ESR 4340M Steel | 40% weight reduction vs. traditional |
Rocket Nozzles | Haynes 230® | 50% longer thermal cycle life |
Structural Fasteners | A-286 Superalloy | Zero stress corrosion cracking |
Future Innovations
- AI-Driven ESR Control: Machine learning optimizes slag composition in real time
- Hybrid Additive Manufacturing: ESR-refined powders for 3D-printed components
- Space-Grade Alloys: Enabling Mars rover components with ESR-processed GRCop-84
Conclusion
Electroslag remelting isn’t just a manufacturing step—it’s an insurance policy for aerospace safety and performance. By delivering unparalleled material purity, fatigue resistance, and thermal stability, ESR ensures components meet the brutal demands of modern aviation while slashing lifecycle costs.